Discover the Safer, More Efficient Cleaning Solution.
Where It Works
We can use the Decamex process on any kind of air cooler with up to 12 tube rows:
- Forced
- Induced
- A frame
Request a Quote
LNG Plant Enhances Fin Fan Cleaning with Decamex®.
In summer 2023, a liquefied natural gas (LNG) plant in the Gulf Coast faced a critical challenge: cleaning 820 fin fans for the first time after five years of operation without using or producing any effluent (water or foam). Recognizing the importance of maintaining efficiency, preventing equipment damage and ensuring safety, the customer started a rigorous selection process of a reliable solution provider. CTP Environment was the one chosen for the job.
How It Works
Our experts stand on the underneath existing platform to apply a dry, thin powder to your equipment in our proven, efficient process. We use low-pressure, compressed air – no water! Afterwards, each tube (up to 12) is thoroughly clean, not just the first few tubes in each row.
Benefits
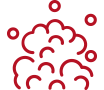
No effluent
- No need for scaffolding or confined space entry
- No need to protect the motor and other critical parts from water or foam
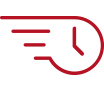
Faster and more efficient
- No production loss
- No need for crane or scaffolding setup
- No need for cleanup time
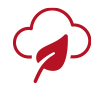
Safe for people and the planet
- Use of biodegradable products
- No generation of effluent
- No water consumption
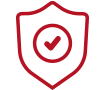
No equipment degradation
- No need for motor protection because our solution is safe for metal
- No corrosion, stress cracking corrosion or abrasion

Better air efficiency and proven ROI
- Decamex delivers a significant increase in air efficiency when compared with the with traditional fin fan cleaning methods.
- The result is rapid ROI.
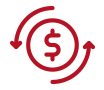
The trusted choice
Hundreds of industrial operators around the world choose Decamex over conventional cleaning solutions.
Compare Types of Cleaning Methods
See the results of extensive equipment testing.
FEATURES | FOAM CLEANING | WATER JETTING | CO2 BLASTING | DECAMEX PROCESS |
Safety and envirent |
|
|
|
|
Time fan is offline to cleanone bundle | 2 hours minimum | 2 hours minimum | Longer than Decamex | 30 minutes maximum |
Cleaning effectiveness |
| Good cleaning of first rows but no penetration through the tube bundles |
|
|
35% clean | 50% clean | 50% clean | 100% clean |